Unlocking Success: Casting Aluminum Made Easy
Unlocking Success: Casting Aluminum Made Easy
Blog Article
The Clear-cut Manual on Light Weight Aluminum Casting Solutions
As industries continue to demand accuracy and top quality, recognizing the nuances of light weight aluminum spreading procedures comes to be paramount. As we browse with this definitive handbook, revealing sector fads and advancements that shape the landscape of light weight aluminum casting solutions, we are advised of the endless opportunities that await those ready to immerse themselves in this detailed craft.
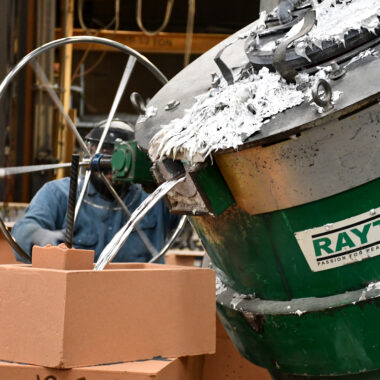
Understanding Aluminum Casting Processes
Checking out the ins and outs of aluminum spreading procedures reveals the precision and intricacy entailed in changing molten metal right into complex elements. Aluminum casting is a thorough production approach that includes the pouring of liquified aluminum right into a mold and mildew to produce a desired form.
Throughout the cooling process, the aluminum takes the shape and solidifies of the mold. What adheres to is careful workmanship to remove any blemishes and fine-tune the component to meet the called for specs. This process requires an eager eye for detail and a deep understanding of metallurgy to make certain the end product's top quality and stability.
Understanding the subtleties of aluminum spreading procedures is essential for generating premium components that meet sector requirements and needs. From aerospace to vehicle sectors, the precision of aluminum spreading plays an important duty in making long lasting and trustworthy parts.
Crucial Tools and Devices
What devices and devices are crucial for accomplishing accuracy and efficiency in aluminum spreading procedures? To ensure successful light weight aluminum spreading, several vital devices and equipment are needed. Crucible heaters play a vital function in melting the light weight aluminum alloys, supplying the liquified metal necessary for casting. Crucibles made from materials like clay graphite or silicon carbide are frequently made use of due to their high heat resistance. Furthermore, a ladle is necessary for moving the liquified steel from the furnace to the molds precisely. Air flow systems are vital to get rid of any kind of fumes or gases generated throughout the spreading procedure, ensuring a safe working environment. Molds, made from materials such as sand or steel, are necessary to shape the liquified steel right into the wanted kind. Other devices like tongs, pouring basins, and cooling down chambers are likewise necessary for taking care of the liquified metal and guaranteeing appropriate solidification. By using these tools and equipment properly, light weight aluminum casting services can attain high accuracy and efficiency in their procedures.
Quality Assurance in Aluminum Spreading
Making certain constant top quality standards is paramount in light weight aluminum casting procedures to satisfy market requirements and client expectations. Quality assurance in aluminum casting involves an organized technique to tracking and assessing every stage of the spreading process to assure the last product's stability. To achieve this, different methods are utilized, such as visual examinations, dimensional checks, non-destructive testing, and product analysis. Aesthetic assessments are conducted to recognize surface area flaws like splits, porosity, or incomplete fills up. Dimensional checks make certain that the casting satisfies specific specifications. Non-destructive testing techniques like X-ray, ultrasonic, or color penetrant assessments can identify internal problems without look at here now harming the part. Material evaluation via spectroscopy or chemical testing verifies the make-up of the light weight aluminum alloy used (casting aluminum). By carrying out rigorous high quality control procedures, light weight aluminum spreading provider can deliver components that adhere to the greatest criteria of efficiency, high quality, and dependability, ultimately satisfying both market policies and client demands.
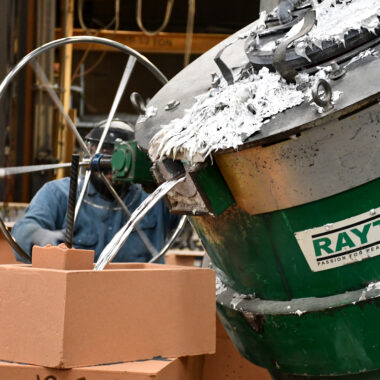
Optimizing Efficiency and Efficiency
To improve functional efficiency in light weight aluminum spreading solutions, maximizing performance and performance is crucial for meeting production needs and preserving affordable benefit in the sector. Implementing lean manufacturing principles, such as reducing waste and improving processes, can dramatically improve overall efficiency. Utilizing advanced technology, like computer-aided design (CAD) software application and automated systems, can boost performance by minimizing manual work and increasing accuracy.
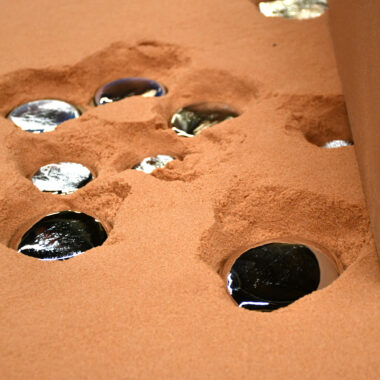
Teaming up very closely with suppliers to guarantee a stable flow of high-grade materials and implementing robust scheduling and stock management systems are also vital techniques for making the most of effectiveness in light weight aluminum spreading solutions. By concentrating on these locations, firms can achieve higher degrees of performance, meet consumer needs effectively, and remain in advance in an open market.
Sector Fads and Developments
In action to the progressing landscape of aluminum casting services, remaining abreast of sector patterns and advancements is critical for keeping an one-upmanship and meeting the vibrant needs of the market. One notable fad in the light weight aluminum casting industry is the increasing concentrate on sustainability and ecological obligation. Firms are embracing greener practices, such as making use of recycled light weight aluminum and executing energy-efficient processes, to straighten with customer expectations and governing demands.
Additionally, advancements in innovation are reinventing aluminum spreading processes. The integration of automation, robotics, and expert system is streamlining manufacturing, improving accuracy, and minimizing lead times. 3D printing is additionally making waves in the market by allowing intricate geometries to be created with better performance and cost-effectiveness.
In addition, there is a growing focus on customization and product customization. With customers seeking distinct and customized items, aluminum casting services are adjusting to supply more versatile production remedies. By embracing these industry patterns and technologies, companies can position themselves for success in a quickly advancing market.
Conclusion
Finally, the manual on light weight aluminum casting services offers a detailed review of the procedures, devices, quality assurance steps, effectiveness look here methods, and sector fads in the area. By recognizing these vital aspects, services can enhance their spreading procedures, make sure high-grade items, and remain affordable on the market. This conclusive handbook acts as an important resource for those associated with light weight aluminum spreading solutions.
As markets continue to demand accuracy and top quality, recognizing the subtleties of aluminum casting procedures comes to be extremely important (casting aluminum). Light weight aluminum casting is a precise manufacturing method that involves the pouring of liquified light weight aluminum into a mold to create a wanted form.Making certain constant high quality standards is extremely important in aluminum casting procedures to satisfy industry needs and consumer assumptions. Quality control in aluminum spreading includes a methodical method to monitoring and reviewing every phase of the casting procedure to ensure the final item's integrity.In verdict, the handbook on light weight aluminum casting services supplies a detailed overview of the procedures, tools, top quality control steps, efficiency methods, and industry patterns in the field
Report this page